Large forgings are generally made through the process of open-die forging. Called open-die because the metal is not laterally confined during forging, as it is during impression or closed-die forging, this process continuously works the starting stock until it reaches its desired shape and proportions, most commonly between flat-faced dies. Read More…
For over 30 years, we have provided metal forged products for a wide variety of industries, including the aerospace, military, food service, medical, and automotive industries. Our customers know they can trust our forgings for quality and affordability.
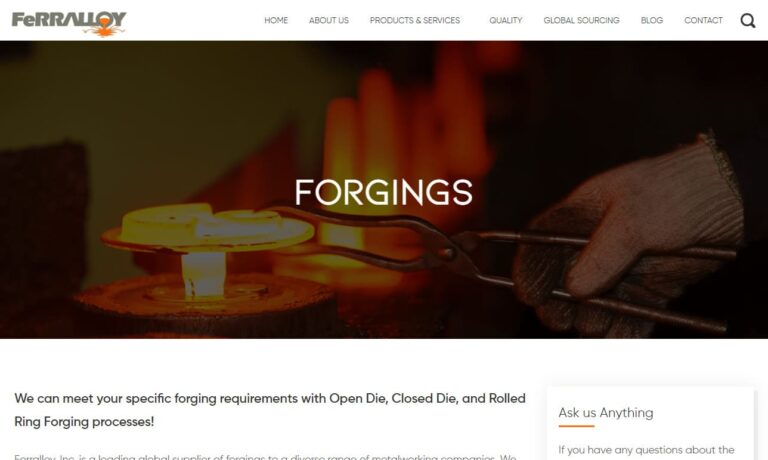
All Metals & Forge Group is your ISO9001:2015 and AS9100D registered forging facility. All Metals provides a wide range of materials, products and services, including discs, shafts, sleeves, cylinders, plates, blocks and many other shapes, both stock and custom, satisfying all of their customers’ requirements. Give All Metals & Forge Group a chance to satisfy your needs— you’ll be glad you...
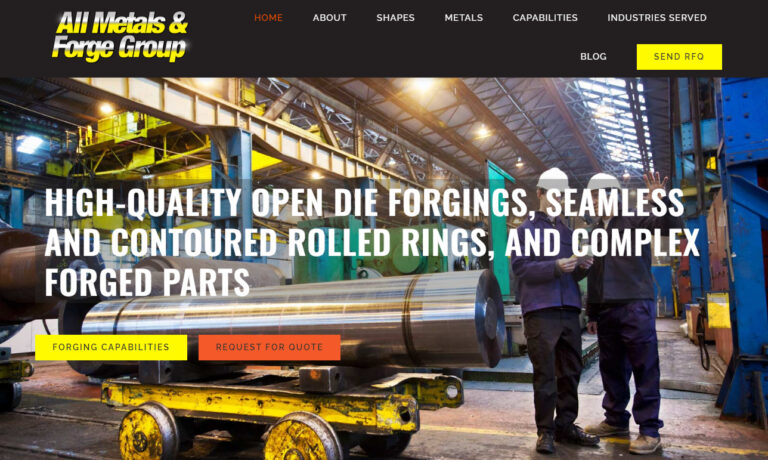
Although we have over 100 years of experience, we are committed to continually expanding our offerings in all industries. We are not content to remain as we are, but we continually work to improve our products and processes each and every day.
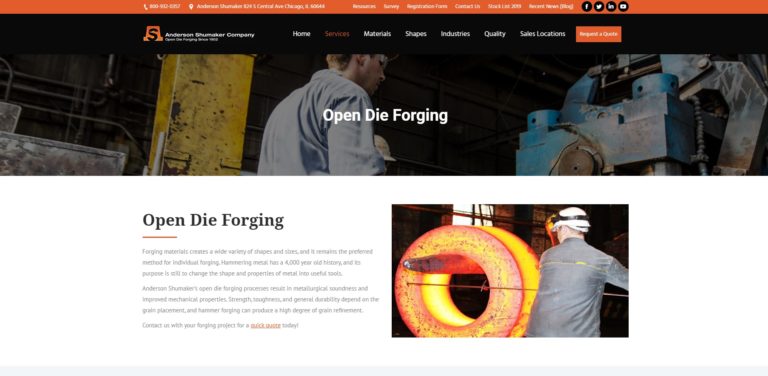
At Lenape Forged Products Corp., we take immense pride in our legacy of delivering high-quality forged products to a diverse array of industries. We specialize in producing precision-forged components that meet the rigorous standards required by our clients. Our extensive range of forgings includes everything from intricate custom parts to high-volume, standardized components, all meticulously...
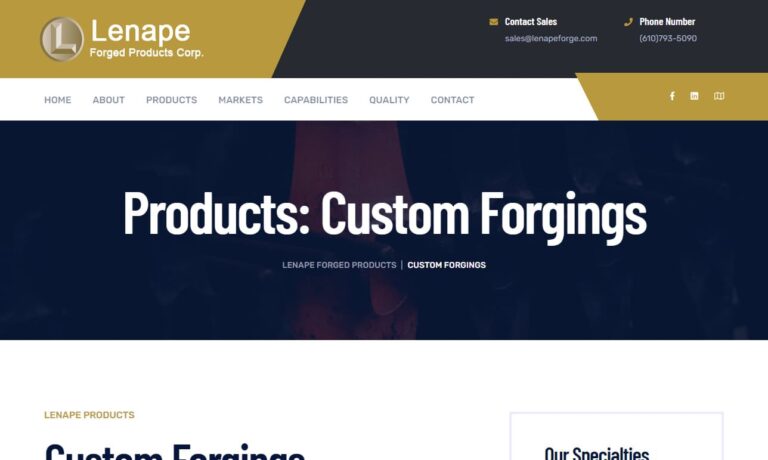
At Bula Forge & Machine, Inc., we are dedicated to delivering exceptional forging solutions that cater to a wide range of industries. Our expertise in the field of forgings is driven by a commitment to precision, innovation, and superior craftsmanship. We specialize in producing high-quality forged components that meet the rigorous demands of our clients.
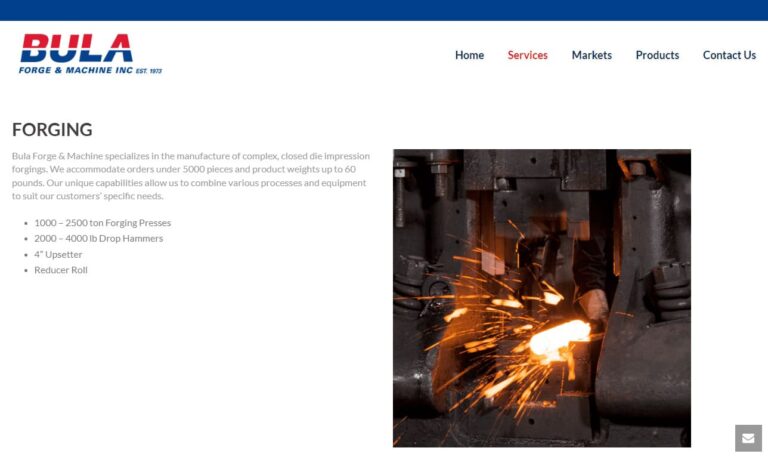
More Large Forging Companies
The many process variations in open die forging make it possible for it to accommodate a broad range of shapes and sizes. The sheer size capability of this type of forging makes it the go-to choice over non-forging when a design requires optimum structural integrity for a large metal part. With this process, the only limit to large forgings is the size of the starting stock. Though often associated with simpler large items, such as bars and rings, open-die forging can in fact produce many custom options without sacrificing structural integrity.
As technology has grown, so have the forging possibilities and capabilities. With the help of advanced computer modeling, many companies can forge incredibly complex shapes. Also, hydraulic presses, weighing upwards of 10,000 tons, can be incorporated into the process to create very large forgings.
Need for large forgings in the U.S. increased in earnest starting in the 1880's and 1890's, when the American government wanted to switch to large, ironclad ships. The defense industry continues to be a market for large forgings, for large weaponry, aerospace technology and the like.
Another fairly early market for large forgings was the electric power industry, which developed after WWII, when the demand for commercial items like wind turbines and generator shafts increased. Currently, among others, large forgings have a strong customer base in industrial equipment and machinery building, mining, commercial nuclear, capital goods such as columns and rams, offshore oil and gas and power generation.